کاربرد اصلی مستربچ آنتی بلاک
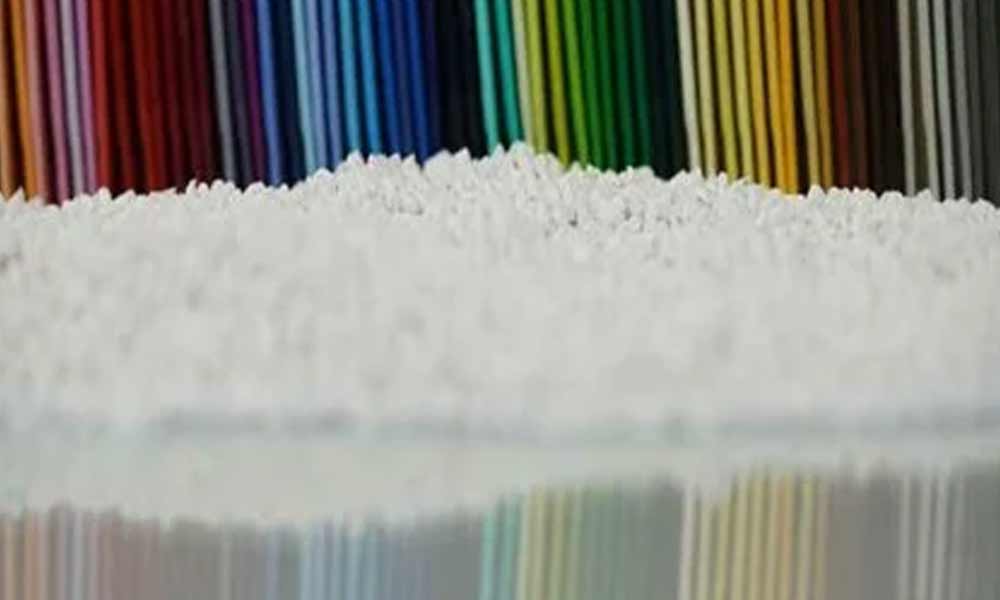
کاربرد اصلی مستربچ آنتی بلاک در صنعت پلاستیک
در صنایع پلاستیک، چالشهایی مثل چسبندگی بین لایههای فیلم پلیمری یکی از دغدغههای مهم تولیدکنندگان محسوب میشود. این پدیده، علاوه بر کاهش کیفیت نهایی محصول، باعث اختلال در فرآیند بستهبندی، افزایش ضایعات و کاهش راندمان خطوط تولید میگردد. برای مقابله با این مشکل، راهکاری فنی و موثر به نام مستربچ آنتیبلاک (Anti-block Masterbatch) وجود دارد که بهعنوان یکی از افزودنیهای کلیدی در تولید فیلمهای پلیمری شناخته میشود.
مستربچ آنتیبلاک چیست؟
مستربچ آنتیبلاک ترکیبی از رزین پایه (Carrier Resin) و افزودنیهای معدنی مانند سیلیس آمورف، تالک یا دیگر فیلرهای تخصصی است که طی فرآیند مستربچینگ با یکدیگر ترکیب شده و به شکل گرانول عرضه میشود. این گرانولها در فرآیندهایی مثل فیلم دمشی (Blown Film) یا فیلم ریختهگری (Cast Film) به پلیمر پایه اضافه میشوند تا از چسبیدن ناخواسته سطوح فیلم به یکدیگر جلوگیری کنند.
سازوکار این مستربچ بر پایه ایجاد ناهمواریهای میکروسکوپی روی سطح فیلم است که موجب کاهش تماس سطحی بین لایهها شده و در نتیجه از چسبیدن آنها جلوگیری میکند.
چرا چسبندگی بین فیلمهای پلاستیکی مشکلساز است؟
فیلمهای نازک پلاستیکی، بهویژه آنهایی که از پلیاتیلن (PE)، پلیپروپیلن (PP) یا PET ساخته شدهاند، در حین تولید یا نگهداری ممکن است بهدلیل فشار رول شدن، حرارت، بار الکترواستاتیکی یا رطوبت، به یکدیگر بچسبند. این چسبندگی باعث بروز مشکلاتی نظیر موارد زیر میشود:
-
سختی در باز کردن رولها هنگام مصرف
-
توقفهای مکرر در خطوط بستهبندی خودکار
-
افزایش زمان آمادهسازی و کاهش سرعت تولید
-
افزایش احتمال پارگی یا ایجاد چین و چروک در فیلم
استفاده از مستربچ آنتیبلاک نهتنها این چالشها را حل میکند، بلکه با بهینهسازی فرآیند، کیفیت محصول نهایی را نیز بهبود میبخشد.
کاربرد اصلی مستربچ آنتی بلاک
کاربرد اصلی مستربچ آنتی بلاک، کاهش چسبندگی بین لایههای فیلم پلاستیکی و بهبود قابلیت باز شدن (Openability) آنهاست.
این ویژگی در صنایعی که از فیلمهای پلیمری استفاده میکنند، بسیار حیاتی است. فیلمهایی که بدون افزودنی آنتیبلاک تولید میشوند، بهویژه در ضخامتهای کم، بهسادگی به یکدیگر میچسبند و در نتیجه استفاده از آنها در فرآیندهای صنعتی بهویژه در بستهبندی مواد غذایی یا دارویی مشکلساز خواهد شد.
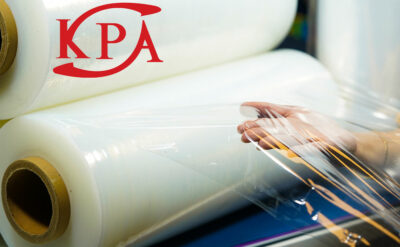
کاربرد اصلی مستربچ آنتی بلاک
کاربرد اصلی مستربچ آنتی بلاک در صنایع مختلف
1.کاربرد اصلی مستربچ آنتی بلاک در صنعت بستهبندی
فیلمهای مورد استفاده در بستهبندی مانند نایلون، لفاف، فیلمهای چندلایه و فیلمهای شرینک، در صورت چسبیدن به هم، باعث اختلال در عملکرد دستگاههای بستهبندی خودکار میشوند. مستربچ آنتیبلاک با ایجاد فاصله میکروسکوپی بین سطوح، از این چسبندگی جلوگیری کرده و سرعت و دقت بستهبندی را بالا میبرد.
این موضوع در بستهبندی مواد غذایی، محصولات دارویی، لوازم بهداشتی و کالاهای مصرفی اهمیت ویژهای دارد.
2.کاربرد اصلی مستربچ آنتی بلاک در فیلمهای گلخانهای و کشاورزی
نایلونهای مورد استفاده در گلخانهها یا فیلمهای کشاورزی باید هنگام نصب بهراحتی باز شوند. چسبندگی این فیلمها میتواند باعث پارگی یا چروکشدگی شده و نصب را سختتر کند. افزودن مستربچ آنتیبلاک در این محصولات، کاربری آنها را آسانتر کرده و بهرهوری را افزایش میدهد.
3.کاربرد اصلی مستربچ آنتی بلاک در صنعت دارویی و بهداشتی
در بستهبندی داروها یا محصولات بهداشتی، باز شدن آسان و بدون ایجاد الکتریسیته ساکن یا جذب ذرات، اهمیت بالایی دارد. مستربچ آنتیبلاک بهویژه در ترکیب با افزودنیهای دیگر مثل آنتیاستاتیک، باعث حفظ کیفیت و پاکیزگی سطح فیلمها میشود.
4.کاربرد اصلی مستربچ آنتی بلاک در صنعت خودروسازی
در برخی از قطعات پلیمری داخلی خودرو یا فیلمهایی که برای محافظت سطوح استفاده میشوند، ویژگی آنتیبلاک باعث بهبود عملکرد مونتاژ و جلوگیری از ایجاد لکه، چسبندگی یا جذب گردوغبار میشود.
5.کاربرد اصلی مستربچ آنتی بلاک در صنعت نساجی (Non-woven)
در تولید منسوجات بیبافت مثل پارچههای اسپانباند، مستربچ آنتیبلاک میتواند به کاهش اصطکاک بین الیاف کمک کرده و روند تولید را روانتر و سریعتر نماید.
مزایای استفاده از مستربچ آنتیبلاک و کاربرد اصلی مستربچ آنتی بلاک در
-
جلوگیری از چسبندگی لایهها در طول تولید و ذخیرهسازی
-
افزایش سرعت ماشینآلات بستهبندی
-
کاهش احتمال آسیب به فیلمها در حین استفاده یا حملونقل
-
افزایش شفافیت و کیفیت سطح فیلم (در صورت انتخاب مستربچ مناسب)
-
قابلیت ترکیب با سایر افزودنیها مثل آنتیاستاتیک، آنتیاکسیدانت و آنتییووی
-
صرفهجویی اقتصادی با کاهش ضایعات و توقف خطوط تولید
نکات مهم در انتخاب مستربچ آنتیبلاک ، کاربرد اصلی مستربچ آنتی بلاک
انتخاب مستربچ آنتیبلاک مناسب، مستقیماً بر عملکرد، کیفیت نهایی فیلم و نیز راندمان تولید تأثیر میگذارد. برای اینکه این افزودنی بیشترین کارایی را در سیستم تولید شما داشته باشد، باید چندین فاکتور فنی و اجرایی را در نظر بگیرید:
1. نوع پلیمر پایه (Carrier Resin)
مهمترین نکته در انتخاب مستربچ، سازگاری رزین پایه آن با پلیمر مورد استفاده در تولید است. بهعنوان مثال:
-
اگر در حال تولید فیلم پلیاتیلن (PE) هستید، مستربچی با پایه PE انتخاب کنید.
-
برای فیلمهای پلیپروپیلن (PP)، مستربچ با پایه PP مناسبتر است.
این تطابق باعث پخش یکنواخت مستربچ در ساختار فیلم و جلوگیری از جدایش یا ایجاد نقاط ضعف مکانیکی در محصول نهایی میشود.
2. اندازه ذرات معدنی (Particle Size)
اندازه ذرات مواد معدنی استفادهشده مانند سیلیس یا تالک، تأثیر زیادی بر عملکرد آنتیبلاک دارد. هر چه ذرات درشتتر باشند، کارایی ضد چسبندگی بیشتر است؛ اما ممکن است باعث کدری یا کاهش شفافیت فیلم شود. در مقابل، ذرات ریزتر ظاهر فیلم را بهتر حفظ میکنند اما ممکن است عملکرد آنتیبلاک ضعیفتری داشته باشند.
پیشنهاد فنی: برای فیلمهای شفاف مانند فیلم بستهبندی مواد غذایی، مستربچهایی با ذرات ریزتر استفاده شود.
3. غلظت و میزان مصرف مستربچ (Dosage)
میزان مصرف مستربچ بسته به نوع محصول، ضخامت فیلم، و شرایط فرآیند متفاوت است. مقدار پیشنهادی معمولاً بین ۱ تا ۵ درصد وزنی نسبت به کل پلیمر مصرفی است. با این حال:
-
فیلمهای ضخیمتر ممکن است به مستربچ کمتری نیاز داشته باشند.
-
فیلمهای نازکتر، مخصوصاً آنهایی که رول میشوند، مستعد چسبندگی بیشتری هستند و ممکن است به غلظت بالاتری نیاز داشته باشند.
در صورت استفاده بیش از حد از مستربچ، ممکن است اثرات جانبی نظیر کدری فیلم یا کاهش خواص مکانیکی ظاهر شود.
4. سازگاری با افزودنیهای دیگر
در بسیاری از کاربردها، مستربچ آنتیبلاک بههمراه افزودنیهای دیگری مثل آنتیاستاتیک، آنتییووی (ضد اشعه ماورا بنفش)، آنتیاکسیدانت، یا آنتیفوگ بهصورت همزمان مورد استفاده قرار میگیرد. در این حالت، ترکیب و تعامل بین افزودنیها باید مورد بررسی قرار گیرد تا تداخلی در عملکرد آنها ایجاد نشود.
نکته مهم: برخی از مستربچهای ترکیبی بهصورت چندکاره طراحی میشوند و همزمان خاصیت آنتیبلاک، آنتیاستاتیک یا آنتیفوگ را دارند.
5. تأثیر بر ظاهر نهایی محصول
یکی از دغدغههای مهم تولیدکنندگان فیلمهای بستهبندی، حفظ شفافیت، براقیت و یکنواختی رنگ سطح فیلم است. افزودن مستربچ آنتیبلاک نباید منجر به ایجاد ذرات قابلدید یا نقاط مات در فیلم شود، بهخصوص در فیلمهای شفاف یا چاپپذیر.
استفاده از مستربچ با توزیع یکنواخت و کنترل دقیق کیفیت در فرآیند تولید، این مشکل را به حداقل میرساند.
6. سازنده و کیفیت مستربچ
تفاوت کیفیت بین برندهای مختلف مستربچ میتواند بسیار قابلتوجه باشد. مستربچهای بیکیفیت یا بدون کنترل دقیق، نهتنها عملکرد مطلوبی ندارند بلکه ممکن است باعث مشکلاتی در فرآیند اکستروژن یا کیفیت نهایی فیلم شوند.
معیارهایی برای انتخاب تأمینکننده مناسب:
-
سابقه و تجربه در تولید مستربچهای صنعتی
-
ارائه آنالیز فنی محصول (TDS، MSDS)
-
پشتیبانی فنی و امکان تنظیم فرمولاسیون طبق نیاز مشتری
-
تطابق با استانداردهای بینالمللی مثل RoHS و FDA (برای کاربردهای غذایی)
7. شرایط نگهداری و ماندگاری محصول
مستربچها، بهویژه آنهایی که حاوی مواد معدنی هستند، باید در محیط خشک و دور از نور خورشید نگهداری شوند تا عملکرد خود را از دست ندهند. رطوبت بالا یا دمای زیاد میتواند باعث ایجاد کلوخه، افت کیفیت یا عدم یکنواختی در زمان مصرف شود.
جمعبندی
مستربچ آنتیبلاک یکی از افزودنیهای کلیدی در صنعت پلیمر است که با هدف بهینهسازی عملکرد فیلمهای پلاستیکی و کاهش چسبندگی بین لایهها استفاده میشود. این افزودنی ساده اما مؤثر، نقش بزرگی در افزایش بهرهوری، کاهش ضایعات و بهبود کیفیت نهایی محصول ایفا میکند.
در صنایع بستهبندی، کشاورزی، بهداشتی، نساجی و حتی خودروسازی، استفاده صحیح و اصولی از مستربچ آنتیبلاک میتواند تأثیر مستقیم بر کیفیت نهایی و عملکرد محصول داشته باشد. در نتیجه انتخاب مستربچ مناسب، از تامینکنندهای معتبر، گامی مهم در مسیر تولید حرفهای و صنعتی خواهد بود.
برای کسب اطلاعات بیشتر و خرید انواع مستربچهای تخصصی مانند مستربچ آنتی بلاک و مستربچ کمک فرایند، به وبسایت کاوش پلیمر البرز مراجعه کنید.